Summary
If you are a sublimation printing supplier, you may have come across one or more hurdles, such as the transfers coming out dull, blurry, not vibrant, and so on. Sublimation printing is the type of printing that requires continuous learning, experimenting, and knowledge upgrade. It involves many other manufacturing processes other than the usual printing process.
The more you train in this area, and the more you experience it, the more likely you will face challenges and eventually overcome them. With the right approach and understanding, you can quickly eliminate and avoid common sublimation printing problems. In this guide, we have compiled some of the most frequent sublimation printing problems, followed by the solutions to fix them. In the later sections, we have also included the six most common sublimation printing problems related explicitly to mugs and their solutions. Let’s start with the six most common sublimation printing problems.
1. Image Ghosting
Image ghosting looks like the second version of your transfer, slightly by the side of your image. It seems like a shadow effect of your transfers. Ghosting generally occurs when the sublimation transfer paper moves even slightly during the sublimation process. This can happen at the time when you open or close your heat press.
How to Fix?
We recommend you tape down your hard material substrates to the sublimation paper. You can use thermal tapes for this purpose. If you’re printing on fabrics, use adhesive spray to keep the paper intact. But, make sure that you remove the transfer paper immediately after pressing. For sublimation, avoid using an auto-open press. The issue with the open press is that generally, they tend to open too fast. Now, this may cause a shift in the paper if you haven’t taped the paper well. So, try not to use the auto-open press.
2. Less Vibrant Transfers
This is one of the most general problems faced by sublimation printing suppliers. The transfers come out less vibrant than expected. There could be a number of reasons for this. The sublimation paper has two different sides. The side that you are supposed to print is typically bright white. The other side is generally off-white. Make sure you’re printing on the correct side, i.e., the bright white one. If you are printing with a sawgrass virtuoso SG400, the bright white side will load face-down in the tray. This could be a sawgrass sg400 color issue too.
What is the Sawgrass SG400 Color Issue?
You need to ensure that you are printing through the custom print drivers. These custom print drivers have color correction programs built into the print control system. The color correction happens at the print driver stage. They are generally easier and less technical to use than an ICC profile.
Sawgrass offers a Print Manager for its printers, making it easier to get great color output with CorelDraw, Adobe Photoshop, Adobe Illustrator, and many more. So, make sure you use the correct color correction program to avoid this issue.
3. Getting Previously Transferred Image on New blank Transfer
This is also a common issue as sublimation ink has the tendency to bleed onto the bottom and top platen of your press during heat transfer.
How to Fix it?
You can fix this by preventing the sublimation ink from getting onto your top and bottom platen. You can use Teflon wrap or Teflon sheets for each platen. Teflon is completely reusable, and you only have to wipe away the excess ink after each press. Another alternative is to use silicone-treated sheets. Make sure you discard these sheets after use.
4. Banding
Banding is a common problem among all digital inkjet printing systems. Banding looks like lines of missing ink on the printout. It can happen due to clogged print head nozzles and streaks of missing ink on the printout. Banding can also occur if the ink dries inside the print heads.
How to Fix it?
You can prevent Banding simply by maintenance. Banding issues generally occur if you are not regularly using the printers. If you print regularly, you are unlikely to face any banding issues. The best way to deal with this is to prevent the ink from running out dry. You can use the head cleaning function of the printres to prevent the ink from running dry. Some printers need to do this manually, while in others, this function is automatic. Lastly, make sure you have plenty of ink in your machine.
5. Blurry and Faded Images
Image fading can usually occur because of the excess of external factors such as time, temperature, pressure, etc. You can prevent it by double-checking the recommended settings of your sublimation blanks. Double-check the temperature of the top platen on your press and make sure that it equals the stated temperature. For this, you can use heat strips.
Image blurring may occur because your substrate received too much time/temperature in the heat press. The image starts to bleed out because of this excess. You can simply resolve it by reducing the time and attempting to print again.
6. Small Dots in the Transfer
Small dots can occur on the output or the finished product due to the presence of excess moisture. You need to get all the moisture out before you print it.
How to fix it?
You can fix this issue simply by pre-pressing the substrates to get the moisture out. Then, let the substrate cool down for some time. After that, place your transfer on and press like normal.
Checklist to Prevent Sublimation Mug Issues
Sublimation mug issues are very common and faced by almost all the suppliers, at least the ones performing it for the first time. The most common issues include the faded, blurry and undesirable outcomes. So, what to do when you start getting less than desirable results? Here’s a checklist for you:
- Sometimes the sublimation black mug looks brown. This can mean that you’re over-pressing the mug. This means that the ink is gassing out and spreading over the area more than it should. Thus, the black color appears brownish.
- Another common issue is that yellow shading appears on the mug. This means that you are actually using inkjet ink instead of sublimation ink. Sublimation ink is essential to sublimate onto mugs.
- If the sublimation black looks green, the issue must be that you’re under-pressing the mug. Make sure you apply just the right amount of pressure to sublimate a mug.
- Sometimes when the quality of the image on the mug is poor, check whether the actual image quality is poor or not. Most of the time this is the case. We recommend setting a DPI of 300 for sublimation printing.
- Besides that, make sure you’re using the correct time, temperature, and pressure for the mug press, as discussed in the above sections of this guide.
Join PrintXpand at Drupa 2024 for an immersive experience!
Visit our booth to witness our powerful web-to-print solutions firsthand, or book a meeting today to explore how we can elevate your printing experience.
So, this was all about sublimation mug issues and how you can solve them.
However, if you want to make your workflow more efficient for your mug business, we can help.
How PrintXpand Can Help
We understand running a mug business comes with its unique set of challenges, but it doesn’t have to be a struggle.
At PrintXpand, we understand the importance of efficiency in managing your mug business, from design to production to customer satisfaction.
Here’s how we can be your trusted partner in optimizing your mug business workflow:
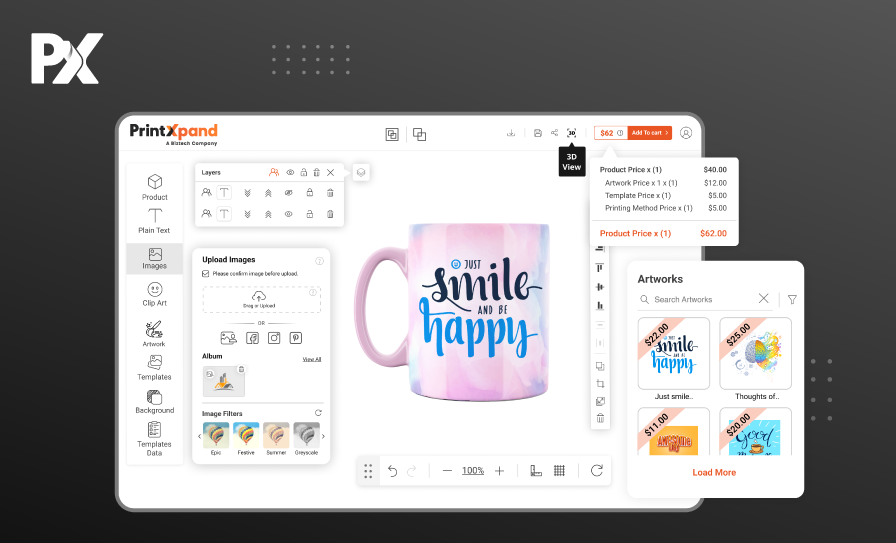
- Streamlined Design Process: Our Mug Designer Tool simplifies the design phase, allowing your customers to effortlessly create personalized mugs with various features, from custom shapes to social media image integration. With our tool, designing becomes a breeze.
- Real-Time Pricing: Say goodbye to pricing headaches. Our live pricing feature provides instant cost calculations, ensuring your customers have full transparency and control over their expenses.
- 3D Visualizations: Boost customer confidence with our 3D preview feature. Your customers can see exactly how their mug designs will look before they make a purchase, reducing the risk of disappointment.
- Comprehensive Image Editing: Our tool offers a robust suite of image editing options and effects, empowering your customers to fine-tune their designs to perfection.
- Mobile Accessibility: Extend your reach with our mobile app, allowing customers to design their mugs on the go. Convenience translates to increased sales and customer satisfaction.
- Vector Output with CMYK: Deliver professional-quality mugs with vector output in CMYK color mode. Your mugs will consistently meet high standards.
- Layer Management: With layer management, designs are kept organized and editable. Your customers can make changes easily, enhancing their overall experience.
- Custom Templates: Custom templates speed up the design process, providing customers with a starting point for their creativity.
- Custom Output: The final product is paramount. Our tool guarantees that your customized mugs meet your specifications and quality standards.
Thus, by incorporating PrintXpand into your mug business workflow, you’re not just solving problems but optimizing your entire operation.
Wrapping Up
So, this was all about sublimation problems, common issues, and how to avoid them. The mug sublimation process is a tricky one as it requires accuracy and has a lot of things to take care of. For any other questions related to sublimation printing, mug sublimation, sublimation print equipment, and so on, you can check out our information station or directly contact our experts to avail free demo for a mug designer tool.
All product and company names are trademarks™, registered® or copyright© trademarks of their respective holders. Use of them does not imply any affiliation with or endorsement by them.